A-H Series™ Threaded Insert
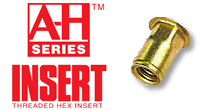
A-H Series™ Threaded Hex Insert features a radius corner hex body. When installed into a corresponding hex hole, the radius corners of the A-H Insert expand and fill the hole corners providing exceptional resistance to spinning in the panel. The A-H Series™ is designed to be used with Grade 5 or Metric Class 8.8/9.8 mating screws.
A-H Series™ Threaded Hex Insert can be installed using AVK’s ARO brand Pneumatic Tools or AVK’s SPP™ Pneumatic/Hydraulic Tools. These tools can be located at any position on your assembly line. The A-H Insert can be installed either before or after finish.
Tabbed Content
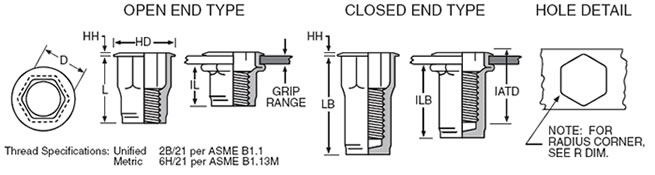

Closed End
Thread area is enclosed eliminating leakage past the threads from either side of the application.

Sealed Head
PVC foam seal is bonded to the underside of the head and when installed provides a weathertight seal. Also available in closed end version.
Step 1
The operator 1/4 turns the AVK fastener on to the tool mandrel and places it into the hole. Operator then presses the top trigger on the tool and the AVK part installs.
Step 2
Once hole fill is complete, the AVK fastener forms its backside flange behind the parent material and the tool stalls.
Step 3
The operator reverses the tool and proceeds to attach the mating component using the appropriate mating hardware. The entire installation sequence of the AVK fastener takes 3 seconds or less.
Notes:
The operator can install the AVK fastener into two different material thickness’. This is the key benefit of the AVK System. You are able to install our products into single, variable or multiple thickness materials without tool adjustment.
During installation the AVK fastener expands within the hole Filling The Hole. This assures excellent spin out resistance and is a feature unique to AVK fasteners.
AVK fasteners are designed to be installed right on your assembly line either before or after paint or finish is applied to your product. This saves space and improves process flow.
AHS3T-420-165
AH | ( ) | ( ) | - ( ) | - ( ) | ( ) | |||||||||||||||||||||||||||||||
|
|
|
||||||||||||||||||||||||||||||||||
|
|
|
|
|
|
* Special order items are subject to minimum order requirements. Contact AVK for details.
THE A-H SERIES™ INSERT - THREAD SIZES![]() UNIFIED(INCH) SIZES |
|||||||||||||
Thread Size | Thread Call Out | Grip Range | Grip Call Out | Hole Size +.006 -.000 | HD ±.010 ±0.25* | HH ±.003 | L ±.015 | D Max. | IL Max. | LB ±.015 | ILB Max | IATD* Max. | R Max. |
---|---|---|---|---|---|---|---|---|---|---|---|---|---|
Thread Size |
Thread Call Out |
Grip Range |
Grip Call Out |
Hole Size (across flats) +.004 -.000 |
HD ±.010 ±0.25* |
HH ±.003 |
L ±.015 |
D Max. |
IL Max. |
LB ±.015 |
ILB Max |
IATD** Max. |
R Max. |
6-32 UNC | 632 | .020-.080 | 80 | .250 | .375 | .027 | .385 | .249 | .295 | .740 | .640 | .575 | .015 |
6-32 UNC | 632 | .080-.130 | 130 | .250 | .375 | .027 | .435 | .249 | .295 | .740 | .580 | .640 | .015 |
8-32 UNC | 832 | .020-.080 | 80 | .250 | .375 | .027 | .385 | .249 | .295 | .740 | .640 | .575 | .015 |
8-32 UNC | 832 | .080-.130 | 130 | .250 | .375 | .027 | .435 | .249 | .295 | .740 | .580 | .640 | .015 |
10-24 UNC | 1024 | .020-.130 | 130 | .281 | .390 | .027 | .435 | .280 | .275 | 1.030 | .845 | .695 | .020 |
10-24 UNC | 1024 | .130-.225 | 225 | .281 | .390 | .027 | .535 | .280 | .275 | 1.030 | .735 | .805 | .020 |
10-32 UNF | 1032 | .020-.130 | 130 | .281 | .390 | .027 | .435 | .280 | .275 | 1.030 | .845 | .695 | .020 |
10-32 UNF | 1032 | .130-.225 | 225 | .281 | .390 | .027 | .535 | .280 | .275 | 1.030 | .735 | .805 | .020 |
1/4-20 UNC | 420 | .027-.165 | 165 | .375 | .510 | .030 | .585 | .374 | .400 | 1.190 | 1.015 | .945 | .040 |
1/4-20 UNC | 420 | .165-.260 | 260 | .375 | .510 | .030 | .685 | .374 | .400 | 1.190 | .915 | 1.085 | .040 |
5/16-18 UNC | 518 | .027-.150 | 150 | .500 | .655* | .035 | .685 | .499 | .530 | 1.445 | 1.235 | 1.045 | .040 |
5/16-18 UNC | 518 | .150-.312 | 312 | .500 | .655* | .035 | .845 | .499 | .515 | 1.445 | 1.220 | 1.170 | .040 |
3/8-16 UNC | 616 | .027-.150 | 150 | .500 | .655* | .035 | .685 | .499 | .530 | 1.445 | 1.235 | 1.045 | .040 |
3/8-16 UNC | 616 | .150-.312 | 312 | .500 | .655* | .035 | .845 | .499 | .515 | 1.445 | 1.220 | 1.170 | .040 |
METRIC SIZES
Thread Size | Thread Call Out | Grip Range | Grip Call Out | Hole Size +0,15 -0,00 | HD ±0,25 ±0,64* | HH ±0,08 | L ±0,38 | D Max. | IL Max. | LB ±0,38 | ILB Max | IATD* Max. | R Max. |
---|---|---|---|---|---|---|---|---|---|---|---|---|---|
M4 x 0,7 ISO | 470 | 0,50-2,00 | 2.0 | 6,35 | 9,53 | 0,68 | 9,78 | 6,35 | 7,49 | 18,80 | 16,26 | 14,61 | ,38 |
M4 x 0,7 ISO | 470 | 2,00-3,30 | 3.3 | 6,35 | 9,53 | 0,68 | 11,05 | 6,35 | 7,49 | 18,80 | 14,73 | 16,26 | ,38 |
M5 x 0,8 ISO | 580 | 0,50-3,30 | 3.3 | 7,14 | 9,91 | 0,68 | 11,05 | 7,10 | 6,99 | 26,16 | 21,46 | 17,65 | ,50 |
M5 x 0,8 ISO | 580 | 3,30-5,70 | 5.7 | 7,14 | 9,91 | 0,68 | 13,59 | 7,10 | 6,99 | 26,16 | 18,67 | 20,45 | ,50 |
M6 x 1,0 ISO | 610 | 0,70-4,20 | 4.2 | 9,53 | 12,96 | 0,76 | 14,86 | 9,50 | 10,16 | 30,23 | 25,78 | 24,00 | 1,0 |
M6 x 1,0 ISO | 610 | 4,20-6,60 | 6.6 | 9,53 | 12,96 | 0,76 | 17,40 | 9,50 | 10,16 | 30,23 | 23,24 | 27,56 | 1,0 |
M8 x 1,25 ISO | 8125 | 0,70-3,8 | 3.8 | 12,70 | 16,64* | 0,89 | 17,40 | 12,70 | 13,46 | 36,70 | 31,37 | 26,54 | 1,0 |
M8 x 1,25 ISO | 8125 | 3,8-7,90 | 7.9 | 12,70 | 16,64* | 0,89 | 21,46 | 12,70 | 13,08 | 36,70 | 30,99 | 29,72 | 1,0 |
M10 x 1,5 ISO | 1015 | 0,70-3,8 | 3.8 | 12,70 | 16,64* | 0,89 | 17,40 | 12,70 | 13,46 | 36,70 | 31,37 | 26,54 | 1,0 |
M10 x 1,5 ISO | 1015 | 3,8-7,90 | 7.9 | 12,70 | 16,64* | 0,89 | 21,46 | 12,70 | 13,08 | 36,70 | 30,99 | 29,72 | 1,0 |
- NOTE 1: Grip range can be affected by parent material density and actual hole size. AVK suggests trial installations to determine optimum grip.
- NOTE 2: Available in additional materials and sizes. Contact AVK for details.
- *Dimensions in minimum grip condition.